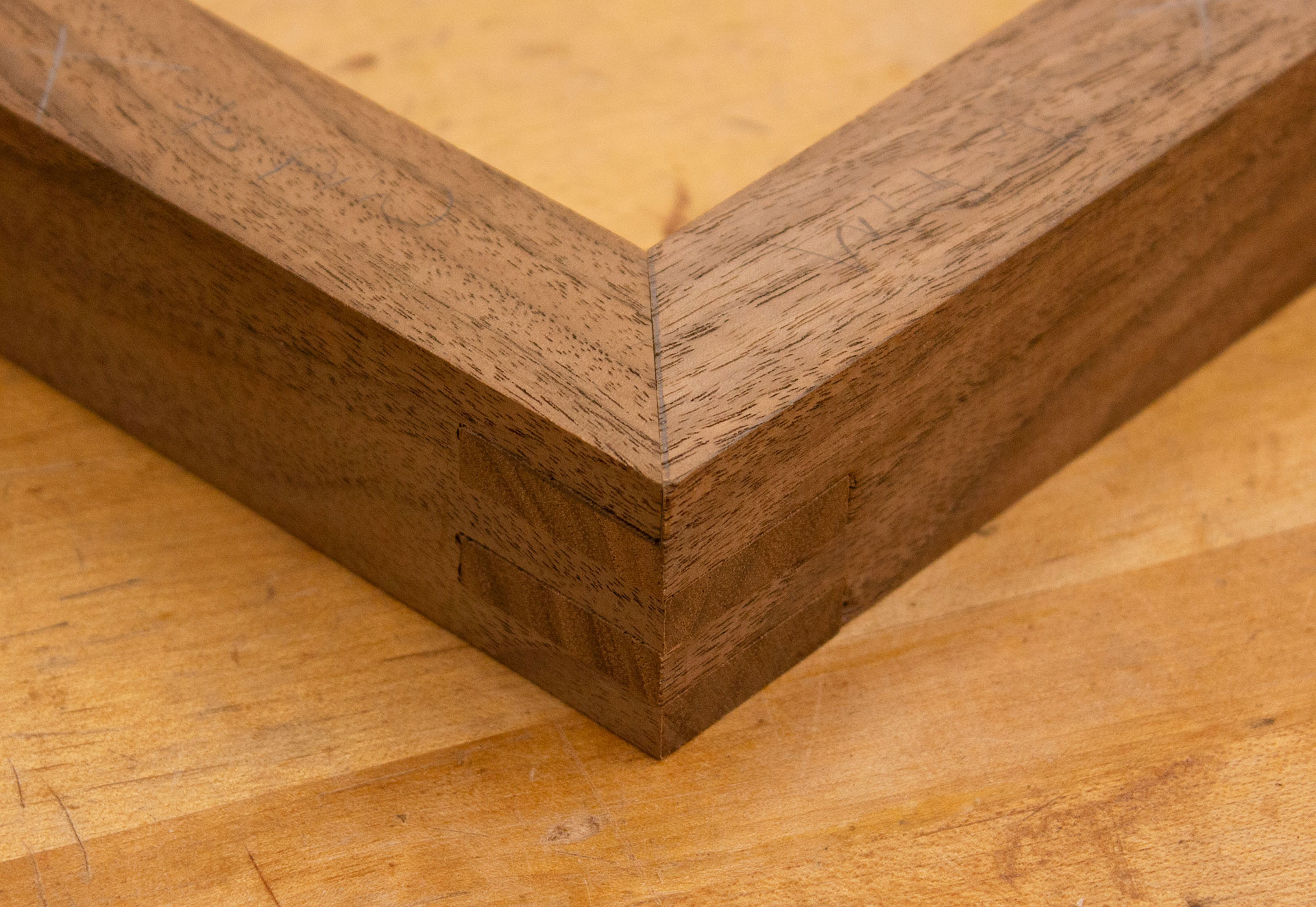
Today, I released a new YouTube video on how to “Build a Tool Wall – No BS Style.” In that video, I show the mitered box joint that I use on each of the corners. But I don’t give you step-by-step instructions on how to make and set up the jig. It’s a big part[…]